Mechatronics & Automotive
Mechatronic systems consist of both mechanical and electrical components. Typical challenges are the high integration of these systems along with the limited computational resources of embedded hardware such as electronic control units (ECUs) in automotive applications. We have a successful history of bridging the gap between theory and practice in close cooperation with industrial partners from the mechatronics and automotive domain.
Contact
Prof. Dr.-Ing. Knut Graichen
Tel.: +49 9131 85-27127
E-Mail | Homepage
Dr.-Ing. Andreas Michalka
Tel.: +49 9131 85-28592
E-Mail | Homepage
Highly integrated mechatronic systems can, for instance, be found in electric drives, power trains, and sensors. Future mechatronic applications will not only involve classical control loops, but will also be equipped with further intelligent and autonomous functionalities such as automatic calibration, fault-tolerant operation and predictive maintenance.
Automotive-related applications such as passenger cars, trucks or agricultural machines involve a multitude of control systems. This ranges from active suspension, traction control, assisted driving up to fully autonomous driving. On the lower level, efficient embedded control implementations are predominant, whereas higher level control loops involve complex decision making in combination with environmental perception.
State-of-the-art modeling approaches of mechatronic systems combine physics-based and data-driven design methods to account for the uncertainties introduced, for example, by wear, aging and serial production spread. A particular expertise of the Chair is to leverage these hybrid models for sophisticated control schemes and the development of tailored algorithms for real-time capable implementations.
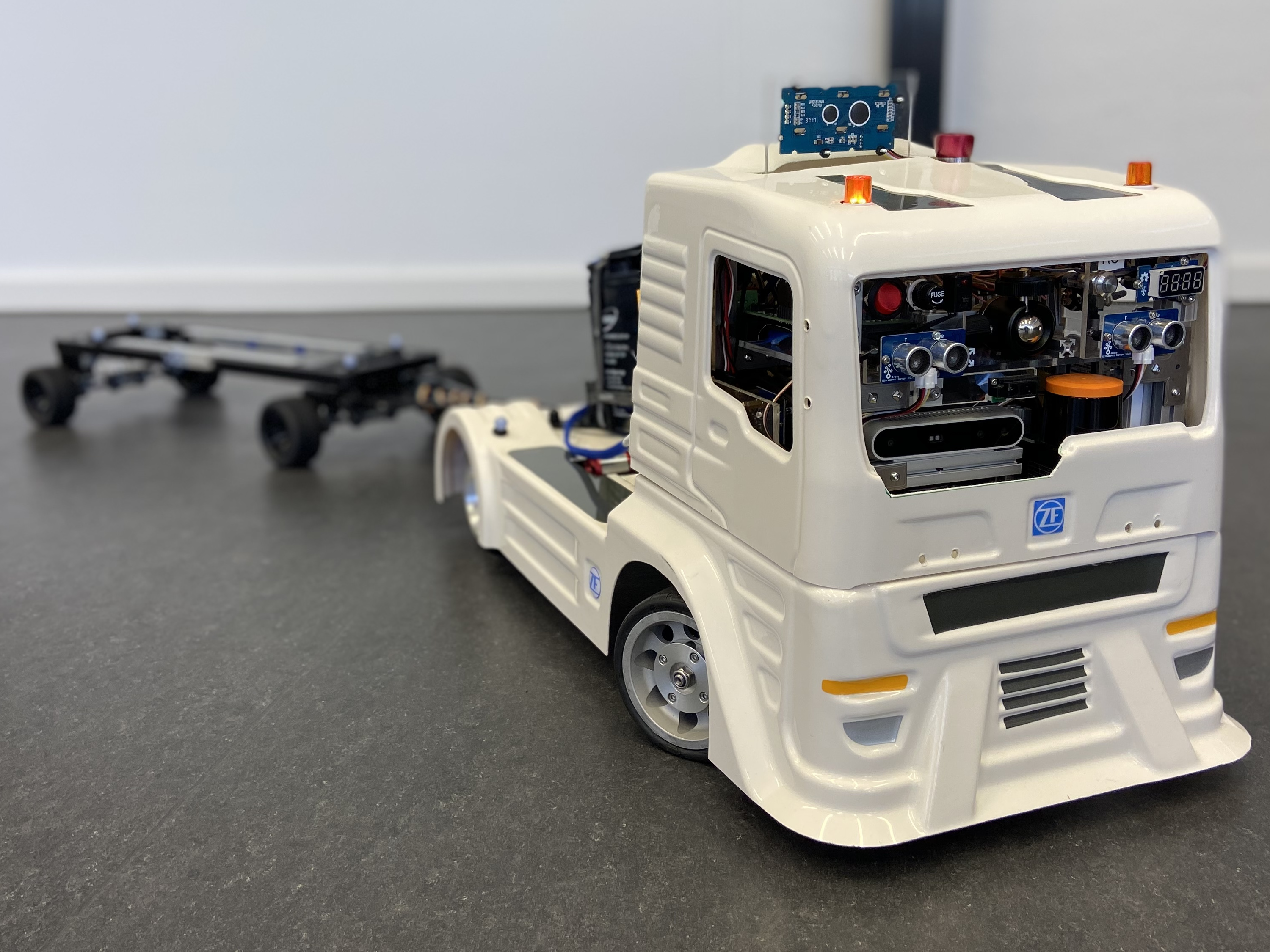
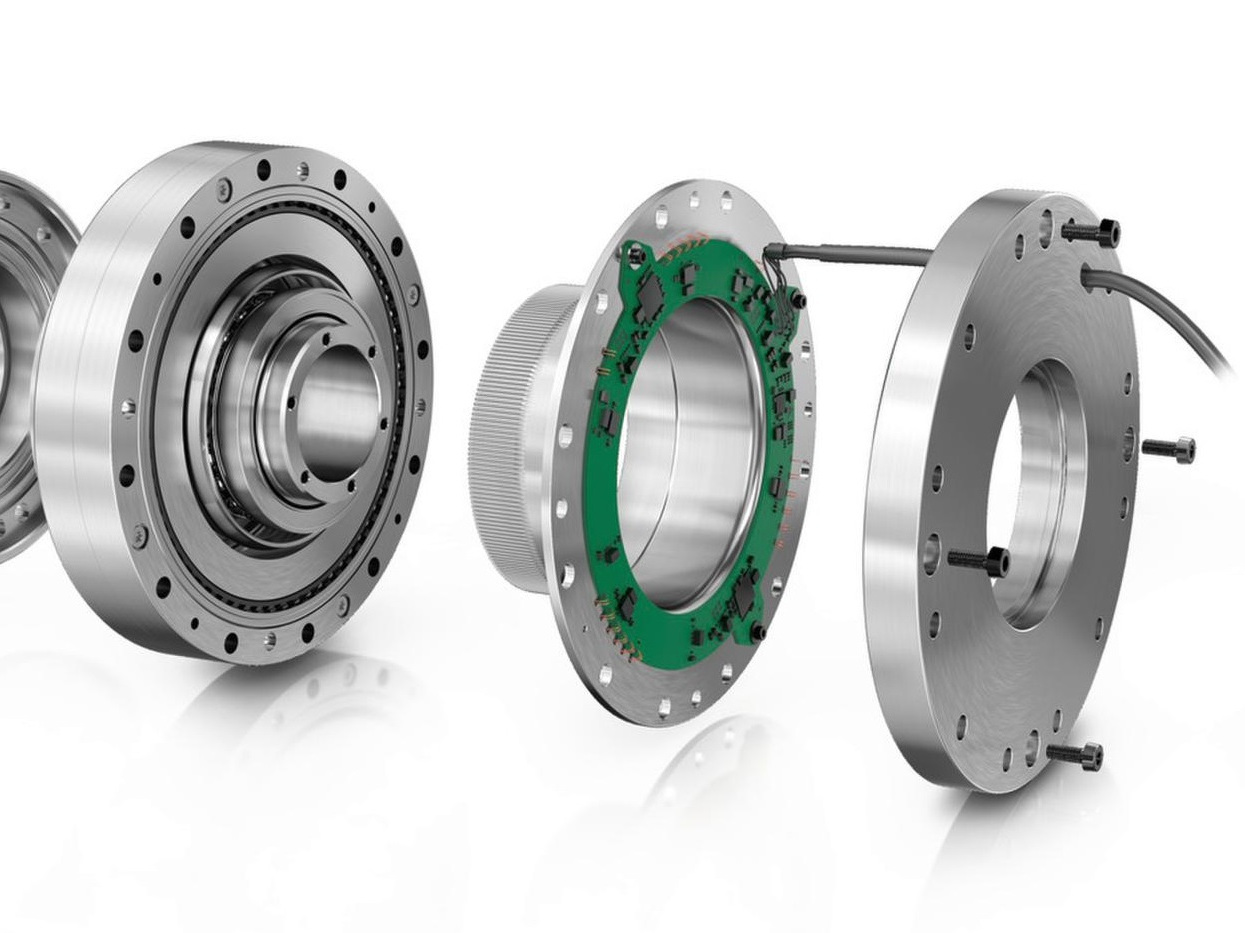

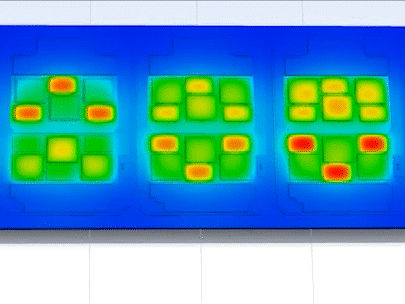
Videos
Related projects since 2021
Funding source: Bayerische Forschungsstiftung
Project leader:
Prof. Dr.-Ing. Knut Graichen
Chair holder
Funding source: Industrie
Project leader:
Prof. Dr.-Ing. Knut Graichen
Chair holder
Funding source: Bundesministerium für Bildung und Forschung (BMBF)
Project leader:
Prof. Dr.-Ing. Knut Graichen
Chair holder
Funding source: Industrie
Project leader:
Prof. Dr.-Ing. Knut Graichen
Chair holder
Funding source: Industrie
Project leader:
Prof. Dr.-Ing. Knut Graichen
Chair holder
Funding source: Industrie
Project leader:
Prof. Dr.-Ing. Knut Graichen
Chair holder
Related publications
- Dahlmann J, Graichen K, Völz A (2024). Ein Konzept zum automatisierten Rangieren von Fahrzeugen mit Anhängern. At-Automatisierungstechnik, 72(4), 354-368. [DOI].
- Dahlmann J, Völz A, Lukassek M, Graichen K (2024). Local predictive optimization of globally planned motions for truck-trailer systems. IEEE Transactions on Control Systems Technology, 32(5), 1555-1568. [DOI].
- Dio M, Demir O, Trachte A, Graichen K (2023). Safe active learning and probabilistic design of experiment for autonomous hydraulic excavators. In 2023 IEEE/RSJ International Conference on Intelligent Robots and Systems (IROS) (pp. 9685-9690).
- Goppelt-Schneider F, Schmidt-Vollus R, Graichen K (2024). Trajectory tracking control for multilevel pressure boosting systems. In 28th International Conference on System Theory, Control and Computing (ICSTCC).
- Harder K, Niemeyer J, Remele J, Graichen K (2023). Hierarchical model predictive control for an off-highway Diesel engine with SCR catalyst. International Journal of Engine Research. [DOI].
- Hartmann P, Graichen K (2025). Learning-based uncertainty-aware predictive control of truck-trailer systems in rough terrain. In 19th IEEE International Conference on Control & Automation (ICCA) (accepted).
- Lukassek M, Dahlmann J, Völz A, Graichen K (2024). Model predictive path-following control for truck–trailer systems with specific guidance points – Design and experimental validation. Mechatronics, 100, 103190. [DOI].
- Löhe K, Reinhard J, Petrasch N, Kallabis S, Graichen K, Mucha M (2024). Work Roll Speed Drop Compensation for Hot Strip Mills Reduces Drivetrain Wear and Increases Strip Quality. In AISTech 2024 Iron and Steel Technology Conference (pp. 1212-1223). Warrendale, PA. [DOI].
- Rabenstein G, Ullrich L, Graichen K (2024). Sampling for model predictive trajectory planning in autonomous driving using normalizing flows. In 5th IEEE Intelligent Vehicles Symposium (IEEE IV 2024) (pp. 2091-2096).
- Reinhard J, Löhe K, Graichen K (2024). Optimal dynamic current control for externally excited synchronous machines. In 2024 IEEE Conference on Control Technology and Applications (CCTA) (pp. 146-152). [DOI].
- Reinhard J, Löhe K, Petrasch N, Kallabis S, Graichen K (2024). Dynamic compensation of the threading speed drop in rolling processes. Journal of Process Control, 137, 103197. [DOI].
- Santer P, Reinhard J, Schindler A, Graichen K (2025). Detection of localized bearing faults in PMSMs by means of envelope analysis and wavelet packet transform using motor speed and current signals. Mechatronics, 106. [DOI].
- Schumann M, Ebersberger S, Graichen K (2023). Online learning and adaptation of nonlinear thermal networks for power inverters. In 49th Annual Conference of the IEEE Industrial Electronics Society (IECON 2023).
- Schumann M, Ebersberger S, Graichen K (2023). Improved nonlinear estimation in thermal networks using machine learning. In IEEE International Conference on Mechatronics (ICM 2023). [DOI].
- Schumann M, Graichen K (2024). PINN-based dynamical modeling and state estimation in power inverters. In 2024 IEEE Conference on Control Technology and Applications (CCTA).
- Snobar F, Michalka A, Horn M, Strohmeyer C, Graichen K (2023). Rack force estimation from standstill to high speeds by hybrid model design and blending. In IEEE International Conference on Mechatronics (ICM 2023). [DOI].
- Snobar F, Michalka A, Horn M, Strohmeyer C, Graichen K (2024). Sensitivity-based moving horizon estimation of road friction. In European Control Conference (pp. 718-724).
- Ullrich L, Buchholz M, Dietmayer K, Graichen K (2024). AI safety assurance for automated vehicles: A survey on research, standardization, regulation. IEEE Transactions on Intelligent Vehicles. [DOI].
- Ullrich L, Buchholz M, Dietmayer K, Graichen K (2024). Expanding the Classical V-Model for the Development of Complex Systems Incorporating AI. IEEE Transactions on Intelligent Vehicles. [DOI].
- Ullrich L, McMaster A, Graichen K (2024). Transfer learning study of motion transformer based trajectory predictions. In 5th IEEE Intelligent Vehicles Symposium (IEEE IV 2024) (pp. 110-117).
- Ullrich L, Völz A, Graichen K (2023). Robust meta-learning of vehicle yaw rate dynamics via conditional neural processes. In 62nd IEEE Conference on Decision and Control (CDC).
- Bergmann D, Harder K, Niemeyer J, Graichen K (2022). Nonlinear MPC of a Heavy-Duty Diesel Engine With Learning Gaussian Process Regression. IEEE Transactions on Control Systems Technology, 30(1), 113-129. [DOI].
- Dahlmann J, Volz A, Szabo T, Graichen K (2022). A Numerical Approach for Solving the Inversion Problem for n-Trailer Systems. In 2022 American Control Conference, ACC 2022 (pp. 2018-2024). Proceedings of the American Control Conference, 2022-June, 2018-2024. [DOI].
- Dahlmann J, Völz A, Szabo T, Graichen K (2022). A numerical approach for solving the inversion problem for general n-trailer systems.. In Proceedings 2022 American Control Conference (ACC) (pp. 2018-2024). [DOI].
- Dahlmann J, Völz A, Szabo T, Graichen K (2022). Trajectory optimization for truck-trailer systems based on predictive path-following control. In 6th IEEE Conference on Control Technology and Applications (CCTA). [DOI].
- Rabenstein G, Demir O, Trachte A, Graichen K (2022). Data-driven feed-forward control of hydraulic cylinders using Gaussian process regression for excavator assistance functions. In 6th IEEE Conference on Control Technology and Applications (CCTA) (pp. 962-969). [DOI].
- Reinhard J, Löhe K, Graichen K (2022). Optimal current setpoint computation for externally excited synchronous machines. In 6th IEEE Conference on Control Technology and Applications (CCTA) (pp. 1319-1326). [DOI].
- Schumann M, Ebersberger S, Graichen K (2022). Dynamic and stationary state estimation of fluid cooled three-phase inverters. In 26th IEEE International Symposium on Power Electronics, Electrical Drives Automation and Motion (SPEEDAM 2022). [DOI].
- Lukassek M, Völz A, Szabo T, Graichen K (2021). Model predictive path-following control for general n-trailer systems with an arbitrary guidance point. In Proceedings European Control Conference (ECC 2021) (pp. 1329-1334). [DOI].
- Bergmann D, Graichen K (2020). Safe Bayesian Optimization under Unknown Constraints. In 59th IEEE Conference on Decision and Control, CDC 2020 (pp. 3592-3597). [DOI].
- Englert T, Graichen K (2020). Nonlinear model predictive torque control and setpoint computation of induction machines for high performance applications. Control Engineering Practice, 99. [DOI].
- Geiselhart R, Bergmann D, Niemeyer J, Remele J, Graichen K (2020). Hierarchical Predictive Control of a Combined Engine/Selective Catalytic Reduction System with Limited Model Knowledge. SAE International Journal of Engines, 13(2). [DOI].
- Geiselhart R, Bergmann D, Niemeyer J, Remele J, Graichen K (2020). Hierarchical predictive control of a combined engine/SCR system with limited model knowledge. SAE International Journal of Engines, 13(2). [DOI].
- Lukassek M, Völz A, Szabo T, Graichen K (2020). Model predictive control for agricultural machines with implements. In Proceedings 28th Mediterranean Conference on Control and Automation (MED) (pp. 387-392). [DOI].
- Mesmer F, Szabo T, Graichen K (2020). Learning feedforward control of a hydraulic clutch actuation path based on policy gradients. In 59th IEEE Conference on Decision and Control (CDC 2020). [DOI].
- Bergmann D, Geiselhart R, Graichen K (2019). Modelling and control of a heavy-duty Diesel engine gas path with Gaussian process regression. In Proc. European Control Conference (ECC 2019) (pp. 1207-1213). Naples (Italy). [DOI].
- Bergmann D, Graichen K (2019). Gaußprozessregression zur Modellierung zeitvarianter Systeme. At-Automatisierungstechnik, 67(8), 637-647. [DOI].
- Mesmer F, Szabo T, Graichen K (2019). Learning methods for the feedforward control of a hydraulic clutch actuation path. In Proc. IEEE/ASME International Conference on Advanced Intelligent Mechatronics (AIM 2019) (pp. 733-738). Hong Kong (China). [DOI].
- Mesmer F, Szabo T, Graichen K (2019). Feedforward control of a hydraulic clutch actuation path. In Proc. European Control Conference (ECC 2019) (pp. 620-626). Naples (Italy). [DOI].
- Englert T, Graichen K (2018). A fixed-point iteration scheme for model predictive torque control of PMSMs. In Proceedings 6th IFAC Conference on Nonlinear Model Predictive Control (NMPC) (pp. 668-673). Madison, WI (USA).
- Harder K, Buchholz M, Späder T, Graichen K (2018). A real-time nonlinear air path observer for off-highway diesel engines. In Proceedings 2018 European Control Conference (ECC) (pp. 237-242). Limassol (Cyprus).
- Käpernick B, Graichen K (2013). Model predictive control of an overhead crane using constraint substitution. In Proceedings 2013 American Control Conference (ACC) (pp. 3979-3984). Washington, DC (USA).
- Käpernick B, Graichen K (2013). Transformation of output constraints in optimal control applied to a double pendulum on a cart. In Proceedings 9th IFAC Symposium “Nonlinear Control Systems” (NOLCOS) (pp. 193-198). Toulouse (Italy).