Robotics
Robotics deals in general with machines that can assist in or perform the execution of tasks such as assembly or machining by industrial robots. Research projects in this area concern, for example, the control of motions and forces in human-robot interaction as well as the planning of paths and trajectories for mobile and collaborative robots.
Contact
Dr.-Ing. Andreas Völz
Tel.: +49 9131 85-61036
E-Mail | Homepage
Prof. Dr.-Ing. Knut Graichen
Tel.: +49 9131 85-27127
E-Mail | Homepage
Robots should move and interact with humans as efficiently as possible. If this includes high velocities or heavy payloads, the nonlinear rigid body dynamics as well as the input constraints need to be taken into account, which leads to a computationally demanding optimization problem. On the other hand, when the robot is in contact with its environment, the rigid body dynamics are often less relevant, but the forces and torques that arise must be considered by the control system. This is especially important for safe human-robot interaction. Here, the challenges include the contact modelling (e.g. stiffness and friction), the safe handling of contact loss, or the selection of controller parameters for different applications. Current research considers model predictive interaction control (MPIC), which refers to MPC with explicit prediction of contact forces and torques, as well as the development of specialized algorithms for solving optimization problems with rigid body dynamics.

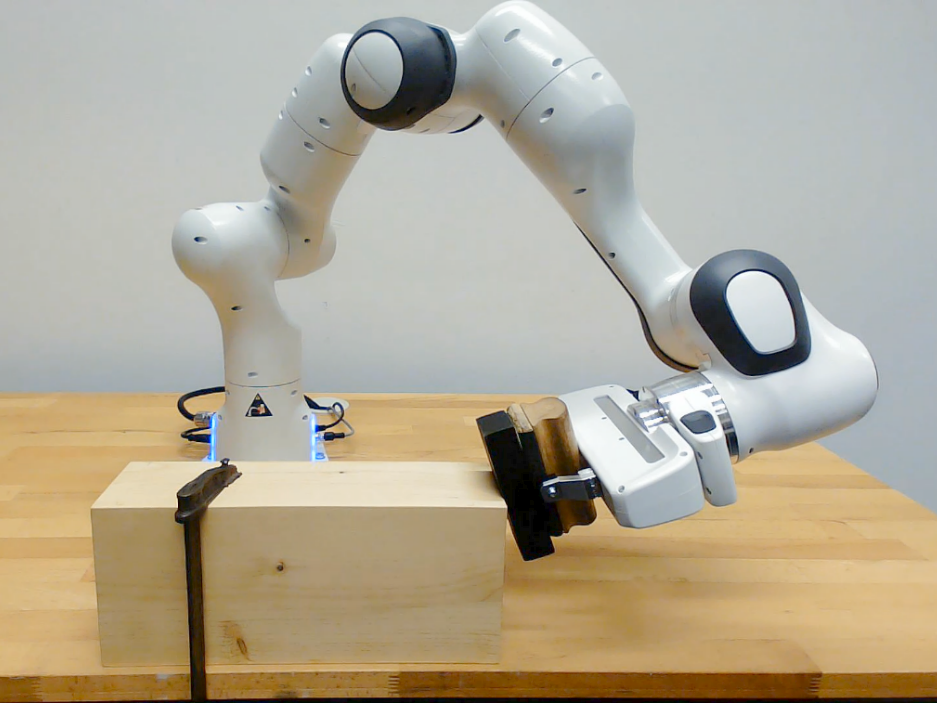
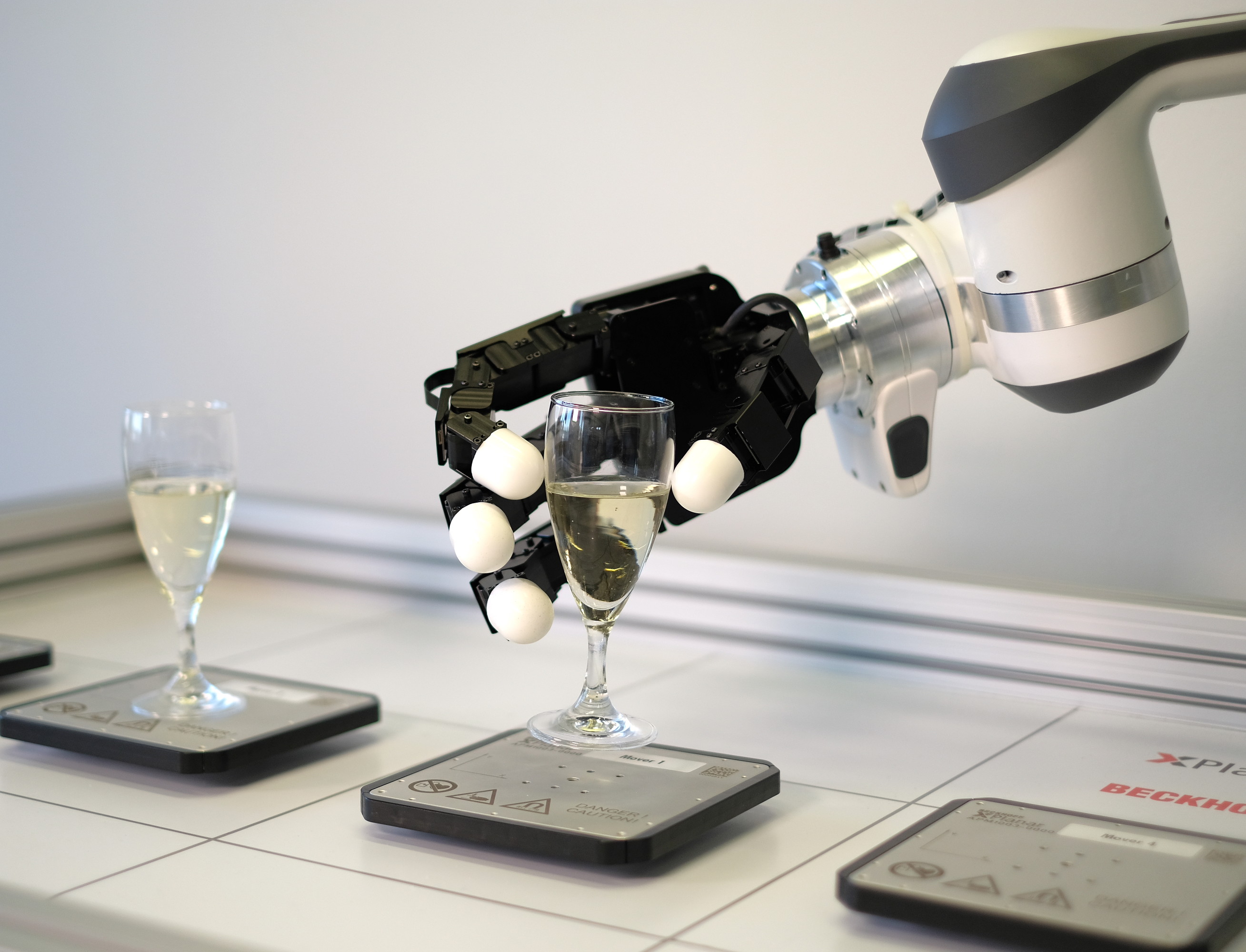
Besides controlling motions, also the planning of paths (geometric description) and trajectories (time information) is a relevant problem for many types of robots. In particular for mobile and collaborative robots, motions should be planned in such a way that they do not cause self-collisions or collisions with obstacles in the environment. Global planners iteratively build a search structure that explores the space of possible motions, whereas local planners only search in the neighborhood of an initial solution. In order to efficiently find high-quality solutions, it is necessary to combine the advantages of both global and local planning methods. Further difficulties arise in dynamic environments, where the future motion of obstacles needs to be predicted or for car-like robots, where the non-holonomic kinematics need to be considered.
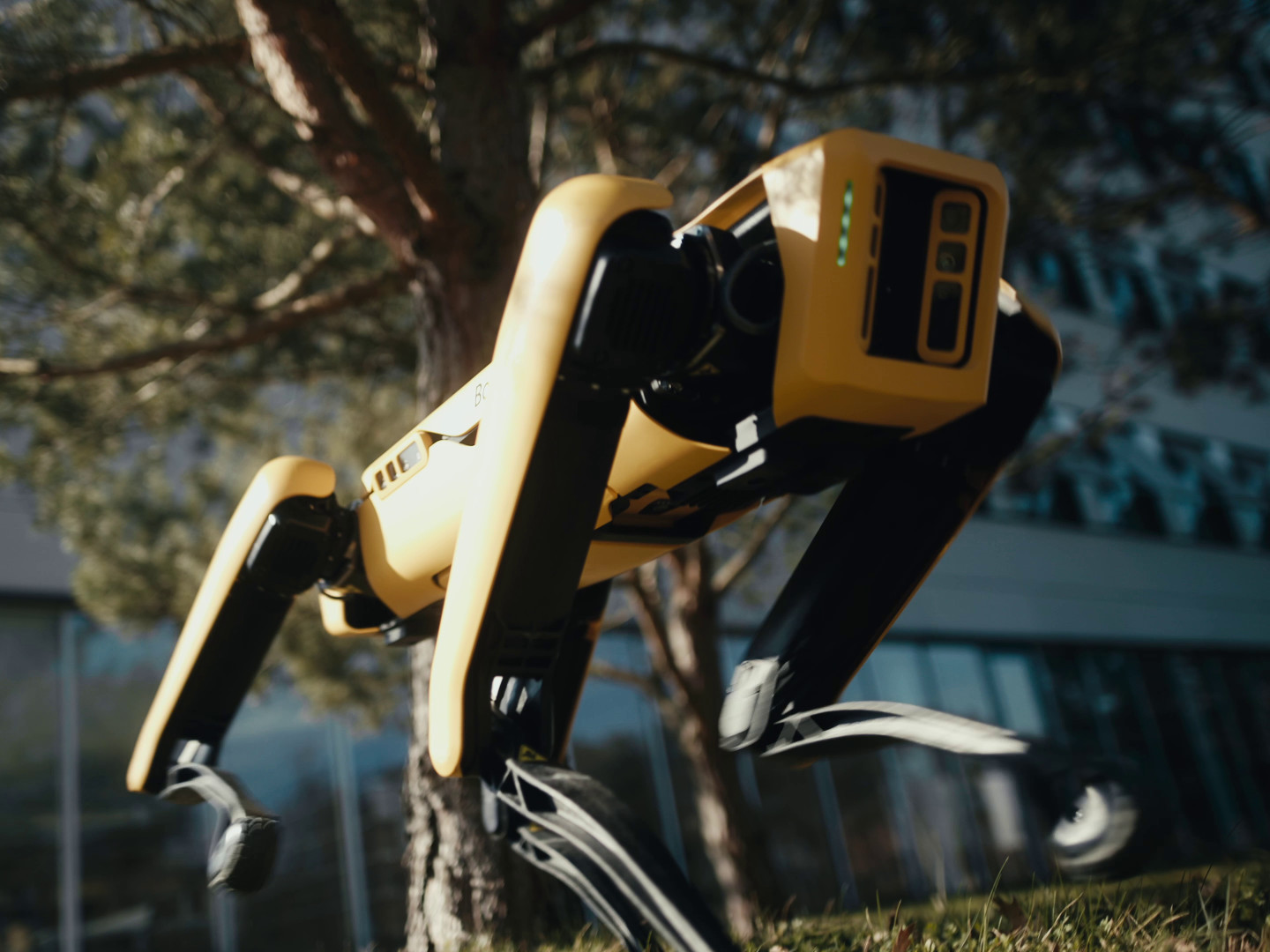
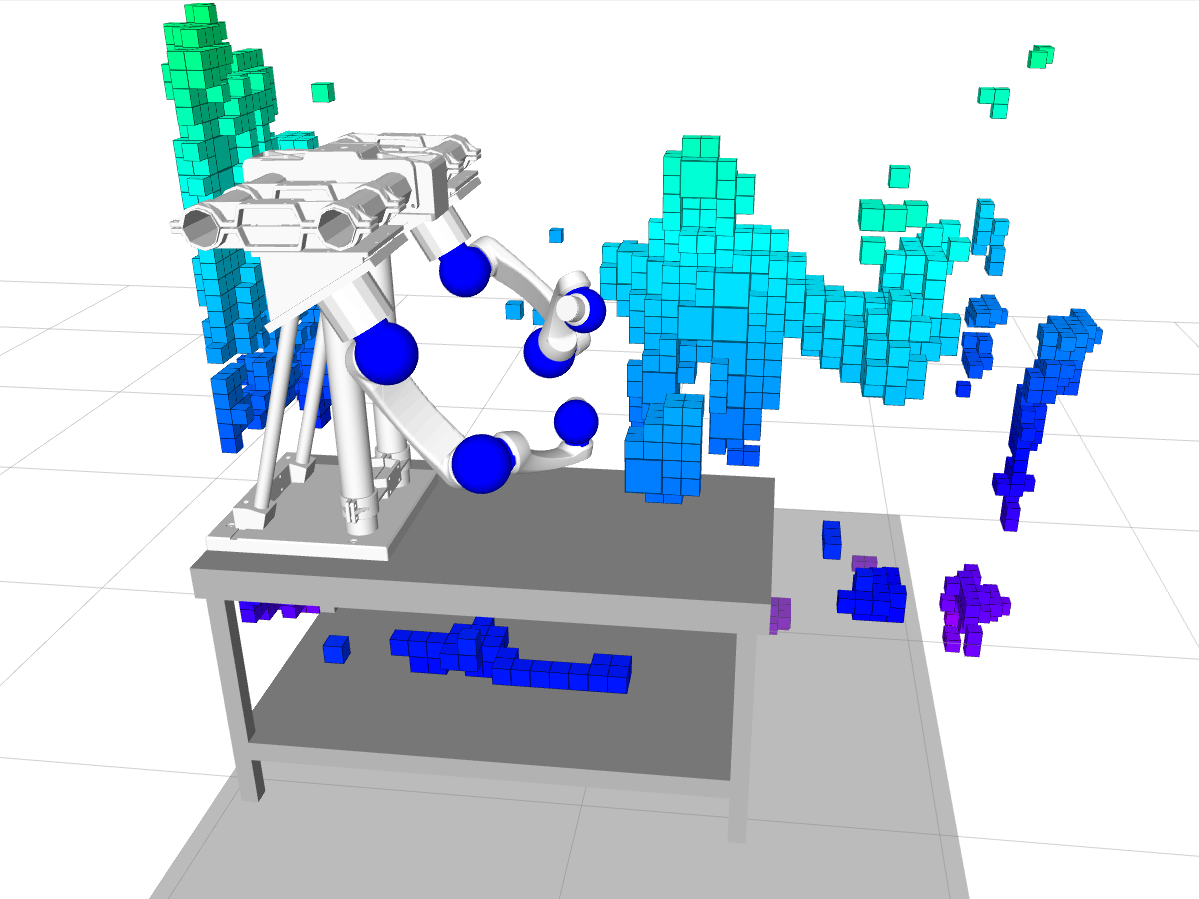
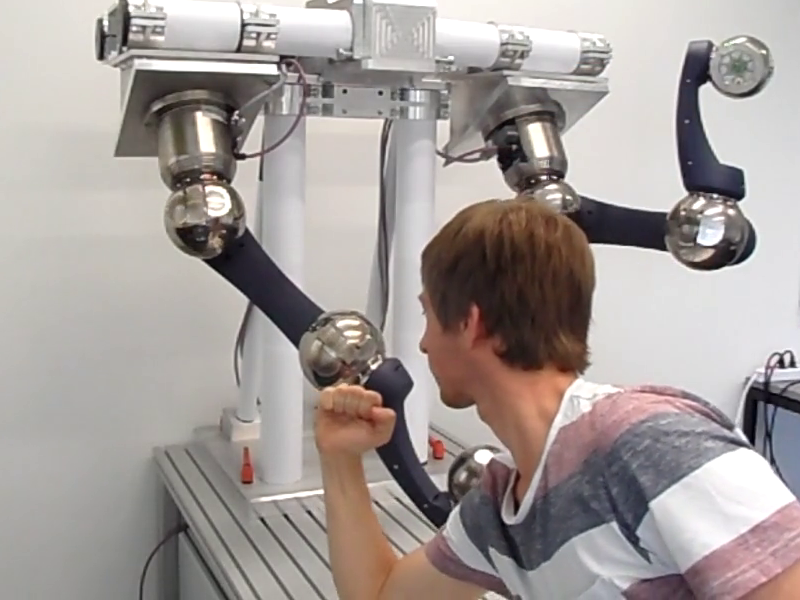
The Chair is equipped with a mobile dual-arm robot as well as a motion capturing system that have been funded by the German Research Foundation (Deutsche Forschungsgemeinschaft, DFG) through the major instrumentation proposal INST 90/1167-1 FUGG. The system enables the experimental validation of planning and control methods for mobile manipulation in workspaces shared with humans. For more information contact Prof. Dr.-Ing. Knut Graichen or Dr.-Ing. Andreas Völz.
Videos
- Writing on a blackboard with chalk – MPIC hybrid force/motion control (IEEE IROS 2020: DOI: 10.1109/IROS45743.2020.9341168)
- Anthropomorphic in-hand manipulation – MPIC for force closure grasping (IEEE CDC 2021)
- Catching objects in flight – MPIC for time-optimal trajectory planning
- Admittance control of the XPlanar system for human-mover interaction
- Collision-free motion planning for a rotating robot with seven degrees of freedom
- Collision-free motion planning for a dual-arm robot with twelve degrees of freedom
- Motion planning for a dual-arm robot with closed kinematics
- Predictive path-following control for continuous replanning with dynamic roadmaps (IEEE RA-L 2019, DOI: 1109/LRA.2019.2929990)
Related projects since 2021
Funding source: Deutsche Forschungsgemeinschaft (DFG)
Project leader:
Prof. Dr.-Ing. Knut Graichen
Chair holder
Precise interactions as part of industrial manufacturing tasks are typically very complex to characterize and implement. One reason for this is the heterogeneity of the task-specific requirements for the motion and control behavior. A direct implementation of the task into a robot program therefore requires highly qualified specialists and is only profitable for large lot sizes. For a flexible applicability and easy (re-)configuration of the robot system, an approach to programming by kinesthetic…
Funding source: Industrie
Project leader:
Prof. Dr.-Ing. Knut Graichen
Chair holder
Funding source: DFG-Einzelförderung / Sachbeihilfe (EIN-SBH)
Project leader:
Dr.-Ing. Andreas Völz
Senior Lecturer
Dual-armrobots offer a high potential for automation technology, as they canbe used to implement tasks that are not possible with one arm alone.This includes in particular the manipulation of large or heavyobjects that exceed the payload of a single arm. Illustrativeexamples are the movement of beverage crates, long boards or pipes,which are also preferably grasped by humans with both hands.
However,cooperative manipulation is particularly challenging, because botharms…
Funding source: Bundesministerium für Wirtschaft und Klimaschutz (BMWK)
Project leader:
Prof. Dr.-Ing. Knut Graichen
Chair holder
Funding source: Industrie
Project leader:
Prof. Dr.-Ing. Knut Graichen
Chair holder
Funding source: Industrie
Project leader:
Prof. Dr.-Ing. Knut Graichen
Chair holder
Related publications
- Dio M, Graichen K, Völz A (2024). Time-Optimal Path Parameterization for Cooperative Multi-Arm Robotic Systems with Third-Order Constraints. In 2024 IEEE/RSJ International Conference on Intelligent Robots and Systems (IROS) (pp. 3043-3048).
- Dio M, Völz A, Graichen K (2023). Cooperative dual-arm control for heavy object manipulation based on hierarchical quadratic programming. In 2023 IEEE/RSJ International Conference on Intelligent Robots and Systems (IROS) (pp. 643-648).
- Gold T, Völz A, Graichen K (2023). Model predictive interaction control for robotic manipulation tasks. IEEE Transactions on Robotics, 39(1), 76-89. [DOI].
- Goller T, Brohm D, Völz A, Graichen K (2024). DMP-based path planning for model predictive interaction control. In European Control Conference (pp. 128-133).
- Goller T, Völz A, Graichen K (2024). A Programming by Demonstration Approach for Robotic Manipulation with Model Predictive Interaction Control. In 2024 IEEE Conference on Control Technology and Applications (CCTA) (pp. 799-804).
- Kißkalt J, Michalka A, Strohmeyer C, Horn M, Graichen K (2025). Estimation of input rotation speed in gauge-sensorized strain wave gears. In 2025 IEEE Conference on Control Technology and Applications (CCTA).
- Kißkalt J, Michalka A, Strohmeyer C, Horn M, Graichen K (2025). Model-based fault simulation and detection for gauge-sensorized strain wave gears. In 11th Vienna International Conference on Mathematical Modelling (MATHMOD 25) (pp. 271 – 276). [DOI].
- Rabenstein G, Völz A, Graichen K (2025). Cable Manipulation for Contact Shaping Tasks using Elastic Rods. In IEEE International Conference on Advanced Robotics and Mechatronics (ICARM).
- Rohrmüller M, Beckerle P, Graichen K, Malvezzi M, Pozzi M (2023). In-Hand Manipulation with Synergistic Actuated Robotic Hands: An MPC-Based Approach. In 22nd IEEE-RAS International Conference on Humanoid Robots, Humanoids 2023. [DOI].
- Gold T, Römer R, Völz A, Graichen K (2022). Catching objects with a robot arm using model predictive control. In Proceedings 2022 American Control Conference (ACC) (pp. 1915-1920). [DOI].
- Goller T, Gold T, Völz A, Graichen K (2022). Model predictive interaction control based on a path-following formulation. In Proceedings IEEE International Conference on Mechatronics and Automation (ICMA) (pp. 551-556). [DOI].
- Lamprecht A, Steffen D, Nagel K, Häcker J, Graichen K (2022). Online Model Predictive Motion Cueing With Real-Time Driver Prediction. IEEE Transactions on Intelligent Transportation Systems, 23(8), 12414-12428. [DOI].
- Snobar F, Reinhard J, Huber H, Hoffmann M, Stelzig M, Vossiek M, Graichen K (2022). FOV-based model predictive object tracking for quadcopters. In 9th IFAC Symposium on Mechatronic Systems (Mechatronics 2022) (pp. 13 – 18). [DOI].
- Burk D, Völz A, Graichen K (2021). Experimental validation of the open-source DMPC framework GRAMPC-D applied to the remote-accessible robotarium. In IEEE International Conference on Mechatronics and Automation (ICMA). [DOI].
- Gold T, Rohrmüller M, Völz A, Graichen K (2021). Model predictive interaction control for force closure grasping. In 2021 IEEE Conference on Decision and Control (CDC) (pp. 1018-1023). [DOI].
- Lamprecht A, Emmert T, Graichen K (2021). Learning-based driver prediction for MPC-based motion cueing algorithms. In Driving Simulation Conference Europe 2021 (DSC) (pp. 133 – 140).
- Lamprecht A, Steffen D, Häcker J, Graichen K (2021). Potential der modellprädiktiven Regelung für Fahrsimulatoren. At-Automatisierungstechnik, 69(2), 155-170. [DOI].
- Völz A, Graichen K (2021). Gradient-based nonlinear model predictive control for systems with state-dependent mass matrix. In 2021 IEEE Conference on Decision and Control (CDC), accepted. [DOI].
- Gold T, Lomakin A, Goller T, Völz A, Graichen K (2020). Towards a Generic Manipulation Framework for Robots based on Model Predictive Interaction Control. In IEEE International Conference on Mechatronics and Automation (ICMA) (pp. 401 – 407). [DOI].
- Gold T, Völz A, Graichen K (2020). Model Predictive Interaction Control for Industrial Robots. In 21st IFAC World Congress (pp. 10026 – 10033). [DOI].
- Gold T, Völz A, Graichen K (2020). Model Predictive Position and Force Trajectory Tracking Control for Robot-Environment Interaction. In 2020 IEEE/RSJ International Conference on Intelligent Robots and Systems (IROS) (pp. 7397-7402). [DOI].
- Graichen K, Völz A (2020). Prädiktive Pfadfolgeregelung für die kollisionsfreie Bewegungsplanung von Robotern. At-Automatisierungstechnik, 68(7), 557-570. [DOI].
- Völz A, Graichen K (2020). Prädiktive Pfadfolgeregelung für die kollisionsfreie Bewegungsplanung von Robotern. At-Automatisierungstechnik, 68(7), 557-570. [DOI].
- Gold T, Völz A, Graichen K (2019). External torque estimation for an industrial robot arm using joint torsion and motor current measurements. In Joint Conference 8th IFAC Symposium on Mechatronic Systems (MECHATRONICS) and 11th IFAC Symposium on Nonlinear Control Systems (NOLCOS) (pp. 879-884). Vienna (Austria). [DOI].
- Lamprecht A, Steffen D, Häcker J, Graichen K (2019). Comparison between a Filter- and an MPC-based MCA in an Offline Simulator Study. In Driving Simulation Conference & Exhibition (DSC) (pp. 101-107).
- Lamprecht A, Steffen D, Häcker J, Graichen K (2019). Optimal control based reference generation for model predictive motion cueing algorithms. In 3rd IEEE Conference on Control Technology and Application (CCTA 2019) (pp. 203-208). Hong Kong (China). [DOI].
- Völz A, Graichen K (2019). A predictive path-following controller for continuous replanning with dynamic roadmaps. IEEE Robotics and Automation Letters, 4(4), 3963-3970. [DOI].
- Graichen K, Hentzelt S (2015). A bi-level nonlinear predictive control scheme for hopping robots with hip and tail actuation. In Proceedings 2015 IEEE/RSJ International Conference on Intelligent Robots and Systems (IROS 2015) (pp. 4480-4485). Hamburg (Germany).
- Lamprecht A, Häcker J, Graichen K (2018). Constrained motion cueing for driving simulators using a real-time nonlinear MPC scheme. In Proceedings 2018 IEEE/RSJ International Conference on Intelligent Robots and Systems (pp. 7466-7471). Madrid (Spain).
- Völz A, Graichen K (2017). Composition of dynamic roadmaps for dual-arm motion planning. In Proceedings 2017 IEEE International Conference on Advanced Intelligent Mechatronics (AIM 2017) (pp. 1242-1248). Munich (Germany).
- Völz A, Graichen K (2018). Computation of collision distance and gradient using an automatic sphere approximation of the robot model with bounded error. In Proceedings 50th International Symposium on Robotics (ISR) (pp. 322-329). München (Germany).
- Völz A, Graichen K (2016). Distance metrics for path planning with dynamic roadmaps. In Proceedings 47th International Symposium on Robotics (ISR) (pp. 126-132). München (Germany).
- Völz A, Graichen K (2018). An optimization-based approach to dual-arm motion planning with closed kinematics. In Proceedings 2018 IEEE/RSJ International Conference on Intelligent Robots and Systems (pp. 8346-8351). Madrid (Spain).